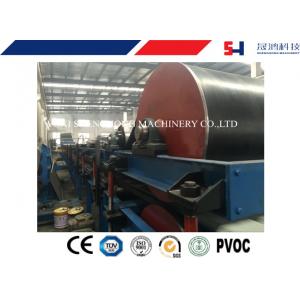
Add to Cart
Euro standard Sandwich Panel Production Line for Construction Use
Our PU sandwich panel has high strength and durability of insulating ability. In addition, we use the PIR (Poly Isocyanurate) which it has the resistance to flame so the panel has the high resistance to flame. Also HCFC-14b the blowing unit as well as the Pentane the eco-friendly material will make more safety and better environment as it’s the “GREEN” unit.
Specification
1. Producing speed | Min. 2meter/min ~Max. 15meter/min | |
2. Length of Double belt conveyor | 20~40meter | |
3. Factory Electricity | 380V x 50Hz x 3Ph (User’s choice available) | |
4. Controlling Electricity | A.C. 220V (User’s Choice Available) | |
5. Factory’s Area | 130~150(Length) x 30m(Width) x 6m(Height) | |
6. Pressure of compressed air | Over 6 bar required | |
7. Production | 4~5 person |
The general specification of PU panel produced
1. Panel length | Min. 2,000mm in auto mode | |
Max. 18,000mm (±3mm) | ||
2. Effective width | 1000mm for roof | |
600mm~1200mm for normal wall | ||
3. Panel thickness | Available thickness from 30~200mm | |
(depended upon heights of the side sealing block.) | ||
4. Top and Bottom layer | Pre-painted Galvanized coil | |
For ASTM A 526-85, JIS G 3302 SGCC | ||
Thickness = 0.4mm ~ 0.7mm | ||
5. insulation | PUR hardened and PIR / Pentane | |
6. Density of Insulation | 30kg/m3 ~ 50kg/m3 |
Un-coiler is a device that inputs steel coil to the upper and lower parts of sandwich panel to feed it stably.
The mandrel type operated automatically by a hydraulic and it’s convenient to control and sophisticated. 2+2 system production equipment unit doesn’t need to stop to load the new coil set, which it helps to continue to produce high capacity of panels.
It is a device that continuously gives shape to sandwich panel as steel coil fed from Un-coiler is engaged between the upper and lower sections of a metal roller.
Usually it makes the beautiful and delicate shape of variety wall and roof type panel. It designed in cassette type and rail way wheel type to easily change to make different shapes
It consists of the nozzle and pump that spray polyurethane solution, a tank that stores solution, various catalysts and gas, and a traverse that enables to spray PU solution evenly, and the device is designed considering high precision and the reliability of maintenance. A convenient control panel is equipped with for users’ easy control of various data required for foaming process.
It equipped with a convenient control panel (Control panel) so that you can easily adjust the various data required for the firing process.
It is a device that makes the shape of sandwich panel applying constant pressure and heat to the upper and lower steel plate foamed with polyurethane.
It designed in perfect structure that has a stiffness and durability and as well as the side blocks to enable the rapid of product replacement.
A device that cuts sandwich panel fabricated at Laminating Unit to the length desired by users using a band saw.
Different types cutting such as wheel cutting and band saw cutting has developed to correspond for the customer’s needs.
In case that a certain time is required till completely hardening since polyurethane sandwich panel is thick, Cooling Conveyer enables to allow sufficient hardening time prior to stacking and packing panels.
As is a device that automatically stacks the finished panels, the quantity desired by users can be loaded continuously by loading pattern of vacuum suction plates or lift conveyor And in case of roofing material, cross stacking is available, if necessary.
A device that packs panels loaded at Auto Stacking Unit with plastic wrap on 4 sides or 6 sides and discharges them.
Applying pallet systems to insert the EPS block automatically and it makes handy for cargo transportation and storage the panels.
Machine show